One of the challenges with OSHA compliance in health care facilities is understanding the terminology used in OSHA regulations and by OSHA personnel. As mentioned last week, OSHA operates in many different industries, so it uses an “occupational safety” vocabulary, rather than speaking in medical or health care-specific terms. This “language barrier” can cause misunderstanding and result in missed opportunities during OSHA inspections. Understanding OSHA terminology should result in higher compliance rates and fewer citations during an inspection.
Over the next few weeks, we will review specific regulations and common violations. As a starting point, here are some common OSHA terms and how they apply in the long term care (LTC) context:
- Safety Program: A safety program is all actions taken by an employer to promote the safety and health of its employees. An effective safety program should demonstrate hazard identification and assessment, safety policies (whether written or unwritten), employee training, monitoring for infractions, and enforcement of safety policies. A safety program is not one set of documents or policies; it should include any action taken at the facility that keeps employees safe, including many resident-care or CMS-driven policies.
- Hazard: A hazard is defined as any source or situation with the potential to cause an employee harm, damage, or adverse health outcomes. Hazards in the workplace can take various forms, including physical, chemical, biological, ergonomic, and others.
- Hazard Assessment: Hazard assessment involves identifying and evaluating workplace hazards to determine the level of risk they pose to employees. It is the first step in creating an effective safety program and involves analyzing tasks, equipment, and work conditions for potential dangers.
- Controls: Controls in occupational safety refer to the measures implemented to eliminate or minimize hazards. These can include engineering controls (physical changes to the workplace), administrative controls (changes in work policies or procedures), and personal protective equipment (PPE) to protect workers. Controls are analogous to interventions in LTC terminology.
- Hierarchy of controls: OSHA's Hierarchy of Controls is a systematic approach to prioritizing and implementing the most effective measures to control workplace hazards and protect workers. The five levels of the hierarchy, in order of priority, are Elimination, Substitution, Engineering, Administrative and lastly, Personal Protective Equipment. The hierarchy of controls serves as a guide for employers to select the most effective control measures for a specific workplace hazard.
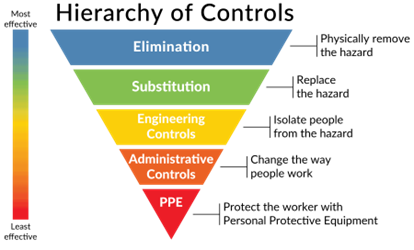
- Training/Communication: Training or communication of workplace safety rules goes beyond normal classroom training. When OSHA talks about training, they are also referring to informal on-the-job training and even signage throughout the building—anything that might tell an employee what the safety requirements are in a particular situation or with a particular resident.
- Monitoring: Refers to a systematic and ongoing assessment to ensure compliance with safety regulations and to identify and address potential hazards. OSHA expects facilities not only to create safety rules and communicate them to employees, but also to monitor to determine whether employees are following the rules.
- Enforcement: Refers to the agency's efforts to ensure compliance with workplace safety and health regulations. OSHA is responsible for enforcing the Occupational Safety and Health (OSH) Act, which establishes and regulates workplace safety standards in the United States.
OSHA enforcement involves several key components, such as Inspections, Citations, Penalties, Abatement and Follow-Up.
- Progressive Disciplinary Policy: A progressive disciplinary policy refers to a series of disciplinary actions that escalate in severity if an employee continues to violate safety policies or regulations.
- Abatement: Abatement refers to the process of reducing or eliminating hazards in the workplace. It involves taking corrective actions to make the workplace safer, such as repairing faulty equipment, implementing safety protocols, or providing appropriate training to employees. Abatement is like a “Plan of Correction” for a state survey.
- Inspection: An OSHA inspection typically occurs on-site, like a state survey, and involves five general steps: opening conference, a walk around inspection, employee interviews, document review, and a closing conference. Except for the opening and closing conferences, OSHA is not required to conduct the steps in any particular order. They might also conduct employee interviews and document review remotely, after they have left the facility.
- Compliance Officer: A compliance officer or “CSHO” is an individual responsible for ensuring that an organization adheres to OSHA regulations and standards. This role involves conducting inspections, assessing compliance levels, and guiding the organization in meeting all necessary safety requirements. The compliance officer is like a surveyor from the state survey agency.
- Recordkeeping: Recordkeeping refers to your OSHA 300 logs and recording of workplace injuries and illnesses. Compliance requires healthcare facilities to keep a detailed log of incidents, which, in theory, allows better hazard analysis and prevention. (See OSHA Standard 29 CFR 1904).
- Reporting: OSHA reporting refers to the obligation of employers to report certain workplace incidents to OSHA within a specified timeframe. Employers are required to report to OSHA within specific timeframes for the following incidents:
- Fatalities: Employers must report any work-related fatalities to OSHA within 8 hours of the incident.
- Hospitalizations: Employers must report any work-related hospitalization, amputation, or loss of an eye to OSHA within 24 hours of the incident
Employers can report incidents to OSHA by phone or through the OSHA website. Of note, employers are required to report “work-
related” COVID-19 fatalities and in-patient hospitalizations to OSHA.
- Sharps: These are defined as any object or device that has a sharp point or edge capable of puncturing, lacerating, or penetrating the skin. Sharps include items such as needles, syringes, scalpels, razor blades, lancets, and other medical devices used for patient care or medical procedures. Sharps will be addressed in more detail when discussing the Bloodborne Pathogen Standard (29 CFR 1910.1030).
- Sharps Log: The Sharps Injury Log is a record of percutaneous injuries from contaminated sharps suffered by employees. A percutaneous injury occurs when a sharp object punctures the skin, such as needlesticks, cuts, or abrasions. The Sharps Injury Log helps employers track and analyze sharps injuries in the workplace, enabling them to identify trends, evaluate the effectiveness of safety measures, and implement preventive measures to reduce the risk of such injuries.
Employers must record all work-related needlestick injuries and cuts from sharp objects that are contaminated with another person's blood or other potentially infectious material.
This is not a complete list of commonly used OSHA terms, but it will hopefully provide some clarity when reviewing OSHA regulations or communicating directly with OSHA. You might also use it as a handy reference tool as we move through this series discussing specific regulations that your facility might need to address.