Introduction
Last week’s article focused on OSHA’s General Duty Clause and how employers have an obligation to protect employees from “recognized hazards” in the workplace. The example we used addressed ergonomics and safe patient handling, which are measures Long Term Care (LTC) Centers must address, even though there is no specific OSHA standard with exact requirements to follow.
OSHA's Personal Protective Equipment (PPE) Standard closely relates to the general duty clause in that it is up to the employer to recognize (or assess) the hazards specific to their center and then control those hazards. However, it is important to note that before we begin to select and distribute PPE to employees, we are required to first conduct a Hazard Assessment.
Hazard Assessment
OSHA states that
“The employer shall assess the workplace to determine if hazards are present, or are likely to be present, which necessitate the use of personal protective equipment (PPE).” The result of the hazard assessment is a selection of PPE for the affected employees. There is no specific format or procedures to follow when conducting a Hazard Assessment. OSHA does, however, reference
nonmandatory guidelines for conducting a hazard assessment and selecting appropriate PPE.
The Hierarchy of Controls
When conducting a hazard assessment to determine PPE, it is important to understand that PPE is only one control measure. In fact, PPE is the
last safety measure to consider as you see in the illustration below. In long term care, we use a mix of measures to minimize occupational hazards. In OSHA’s vocabulary, this mix is known as the
"hierarchy of controls," which consists of FIVE levels: elimination, substitution, engineering controls, administrative controls, and personal protective equipment (PPE).
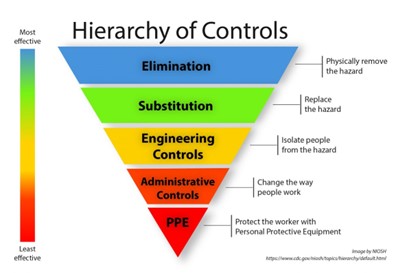
The most effective measures are at the top of the hierarchy, with elimination and substitution being the preferred methods. These involve removing the hazard entirely or replacing it with something less hazardous. Engineering controls come next, focusing on designing and isolating hazards. Examples of such controls in LTC might be negative pressure rooms or barrier walls for protection against airborne infectious agents. Administrative controls involve changing work practices and policies, including infection control procedures and hand-washing protocols.
Personal protective equipment, positioned at the bottom of the hierarchy, is the last line of defense and can include items like gloves, gowns, eye protection, and respiratory protection. The goal is to prioritize controls according to the hierarchy whenever feasible, to ensure the safest working environment.
Although OSHA anticipates facilities to incorporate controls throughout the hierarchy of controls in their hazard assessments, its regulations specifically highlight the importance of conducting hazard assessments for PPE.
Navigating OSHA Standards
The OSHA standard specifically addressing PPE hazard assessments,
29 CFR 1910.132 (See section (d)), provides guidelines for systematically evaluating potential risks and implementing appropriate PPE measures.
Key Elements of PPE Hazard Assessments in LTC Facilities
- Customized PPE Selection: LTC centers require tailored PPE hazard assessments to identify specific risks. Examples include selecting gloves and face shields for personal care tasks and eye protection for administering certain procedures or tasks. Most commonly in LTC, selection of PPE is dictated by standard and transmission-based precautions.
- In-Depth Evaluation of Tasks: Assessments should examine health care tasks, identifying situations requiring specific PPE. For instance, handling medical equipment might necessitate gloves, while respiratory protection, such as N95 respirators, might be required where airborne contaminants are a concern.
- Staff Training on PPE Usage: A hazard assessment should help the employer develop effective training programs on the correct use, limitations, and maintenance of PPE. This allows health care workers to effectively protect themselves and their residents. Training on the proper use of respirators during airborne infectious disease outbreaks is critical.
- Regular Review and Updates: PPE hazard assessments should not be a firm or rigid application. Regular reviews and updates are necessary to account for changes in patient demographics, emerging infectious threats, or alterations in medical procedures. In fact, OSHA requires periodic PPE hazard assessments to be documented through a “written certification that identifies [1] the workplace evaluated; [2] the person certifying that the evaluation has been performed; [3] the date(s) of the hazard assessment; and, which identifies [4] the document as a certification of hazard assessment.
Putting it all together: Hazard Assessment, Hierarchy of Controls and PPE selection
The following table looks at two common LTC hazards: (Bloodborne Pathogens and Airborne Infectious Diseases) and lists possible control measures along the hierarchy of controls.
Hazard Examples and Controls
Control Measure Levels (most to least effective)
| Bloodborne Pathogens
| Airborne Infectious Disease
|
Elimination and Substitution
| Transfer of residents, Hep B vaccinations
| Transfer of residents, quarantined employees, vaccinations
|
Engineering controls
| Needless systems, Sharps with Engineered Sharps Injury Protections (SESIPs), Sharps disposal containers
| Enhanced ventilation systems, HEPA filter units, Isolation of infected residents
|
Administrative controls
| Exposure control plan, training, proper labeling, hand hygiene, standard/transmission precautions, housekeeping | Infectious disease plan, regular testing, training, cohort patients and staff, airborne precautions, visitation restriction
|
Personal Protective Equipment
| As determined by standard and transmission precautions
| Gloves, gown, eye/face, and respiratory protection
|
Conclusion
Much like a resident care plan, workplace hazard assessments are in a state of continuous revision and update. However, the OSHA Standard for Hazard Assessment requires a degree of formality and written records for compliance. As a result, centers should implement an assessment process to create a written document with the OSHA-required data. Regular updates ensure that these assessments remain current and effective in the changing LTC environment.
There are more specific requirements for applications and types of PPE, most notable in the Respiratory Protection Standard requirements, which will be the focus of our next article.