In this article, we will expand on the previous discussion regarding the types of Occupational Safety and Health Administration (OSHA) inspections. Additionally, we will include OSHA procedures to expect and general outcomes of an inspection in a Long Term Care organization.
OSHA inspections can arise from various circumstances, including programmed assessments targeting high-hazard workplaces and unprogrammed responses to imminent dangers, fatalities, or employee complaints. The U.S. Bureau of Labor Statistics (BLS) has identified Healthcare and Social Assistance employers (including skilled nursing facilities and assisted living communities) as having high injury/illness rates, therefore being a target of and OSHA inspection is a high possibility.
Number and rate of nonfatal work illnesses in private industries (bls.gov)
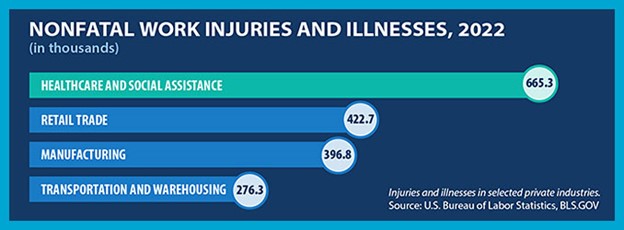
The on-site inspection procedures typically include a comprehensive examination of the facility's safety protocols, focusing on aspects such as infection control, general hazards, and employee training. OSHA compliance officers thoroughly assess areas like recordkeeping, physical hazards, personal protective equipment usage, and emergency response plans. The outcomes of these inspections may result in corrective measures, citations, or, ideally, acknowledgment of a well-maintained and secure environment for the facility employees.
Types of Inspections:
- Programmed Inspections:
- Site-Specific Targeting (SST): OSHA uses a randomized system to target high-hazard workplaces based on their injury and illness rates. This system helps OSHA focus on industries and workplaces with higher risks.
- Emphasis programs: OSHA publishes national, regional, and area emphasis programs identifying industries and specific hazards with historically high injury and illness rates for programmed inspections. Like SST inspections, emphasis program inspections are selected at random from an industry or hazard-specific list. LTC organizations (nursing facilities and assisted living communities) are considered high-hazard industries and have been the subject of several emphasis programs, including, most recently, OSHA’s COVID National Emphasis Program.
- OSHA performs Federal and State inspections routinely. Inspection results for the long term care industry can be found on the OSHA inspection website.
- Unprogrammed Inspections:
- Imminent Danger: OSHA responds immediately to reports of conditions or practices that pose an imminent danger to workers. This type of inspection is given the highest priority.
- Fatalities and Catastrophes: OSHA investigates incidents resulting in fatality or the hospitalization of an employee due to a work-related event.
- Complaints: OSHA often conducts inspections in response to complaints filed by workers or their representatives regarding unsafe or unhealthy working conditions.
- Referrals: Inspections may be initiated based on referrals from other agencies, individuals, or organizations.
- Follow-Up: OSHA may conduct follow-up inspections to ensure that previously cited violations have been corrected.
OSHA Inspection Procedures (On-Site):
- Opening Conference:
- The OSHA compliance officer explains the purpose of the inspection, the scope of the investigation, and the standards that apply.
- The employer and employee representatives are invited to participate in the opening conference.
- Presentation of Credentials:
- The OSHA compliance officer presents their credentials to confirm their identity.
- Walkaround Inspection:
- The compliance officer, accompanied by the employer and employee representatives, conducts a walkthrough of the workplace.
- They inspect for hazards, potential violations, and assess the overall safety of the workplace.
- Employee Interviews:
- The compliance officer may interview employees privately to inquire about workplace conditions, safety practices, and potential concerns.
- Document Review:
- The officer reviews relevant records, such as injury and illness logs, training records, and safety procedures.
- Closing Conference:
- After the inspection, the compliance officer holds a closing conference with the employer and employee representatives.
- Findings, including any violations, are discussed, and the employer is informed of their rights and responsibilities.
Note that the specific procedures may vary based on the type of inspection (programmed or unprogrammed) and the circumstances leading to the inspection.
OSHA Inspection Outcomes:
- Citations and Penalties:
- If violations are found, OSHA may issue citations detailing the specific standards violated and propose penalties. The severity of the violation, good faith of the employer, the employer’s size, and the employer's history of compliance influence the penalties.
- Abatement Period:
- The employer is given a specific period, known as the abatement period, to correct the identified violations. The length of this period depends on the severity of the violation.
- Informal Conference:
- Employers have the option to request an informal conference with OSHA to discuss the inspection results, proposed penalties, and abatement measures. This provides an opportunity for clarification and negotiation.
- Contesting Citations:
- Employers have the right to contest OSHA citations and penalties. This involves filing a Notice of Contest within 15 business days of receiving the citations. Even if the employer participates in an informal conference, this deadline remains and cannot be changed by OSHA.
- Abatement Verification:
- After correcting the cited violations, the employer may be required to provide documentation to OSHA as proof of abatement. This ensures that corrective actions have been taken.
- Follow-Up Inspections:
- In some cases, OSHA may conduct follow-up inspections to verify that the identified hazards have been properly addressed and corrected.
- Employee Notification:
- Employers are generally required to post a copy of the citations at or near the location of the violation for three days or until the violation is abated, whichever is longer. This is to inform employees of the inspection results.
- Training and Improvements:
- OSHA may recommend or require additional employee training or improvements in safety procedures to prevent future violations. These additional steps are typically referred to as “enhanced abatement” and may be used when negotiating a reduced citation.
It's important for employers to address OSHA inspection findings promptly, take corrective actions, and maintain open communication with OSHA throughout the process. Proactive measures to ensure ongoing compliance with safety regulations well before OSHA begins an inspection can help prevent future issues and promote a safer work environment.